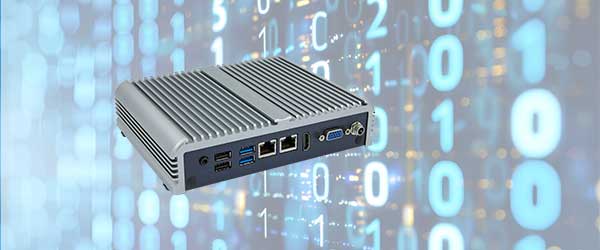
Industrial PCs (IPCs) and Programmable Logic Controllers (PLCs) are both critical for industrial automation, but they serve different purposes. IPCs excel at complex computing, data analysis, and multitasking, while PLCs specialize in real-time machine control and reliability. Choosing the right one depends on your project’s requirements—whether you prioritize flexibility (IPCs) or precision (PLCs).
Key Takeaways
Industrial PCs handle advanced computing, data processing, and scalable automation.
PLCs dominate real-time control, safety-critical tasks, and harsh environments.
Hybrid systems (combining both) optimize efficiency for smart factories.
Defining Industrial PCs and PLCs
What Are Industrial PCs?
An industrial PC is a tough computer made for factories. It is stronger than regular computers and can handle heat, dust, and shaking. These PCs use microprocessors to do hard jobs like studying data, learning patterns, and showing processes. They run on systems like Windows or Linux, making them useful for many tasks.
Industrial PCs are great for jobs needing strong computing and flexibility. They work with advanced software to watch and control many tasks at once. They also use programming languages like Java or C++ for custom automation projects.
What Are PLCs?
A programmable logic controller (PLC) is a small, strong device for controlling machines. It uses a microcontroller and works step-by-step to complete tasks. PLCs are built for real-time control of machines like robots, conveyors, and factory lines.
PLCs use special programming languages like ladder logic, which follow IEC 61131 rules. These rules help different brands work together, saving money and time. PLCs are best for safety systems and places needing reliable performance.
Their Roles in Industrial Automation
Both industrial PCs and PLCs are important in automation. Industrial PCs handle big data tasks and are good for flexible jobs. They connect with SCADA systems to monitor and improve processes in real time.
PLCs are key for machine control. They check things like temperature and pressure to keep machines running well. They also manage safety in risky areas, ensuring smooth and safe operations.
Tip: Using both industrial PCs and PLCs together can give you flexibility and reliability.
Industrial PC vs PLC: Technical and Functional Comparison
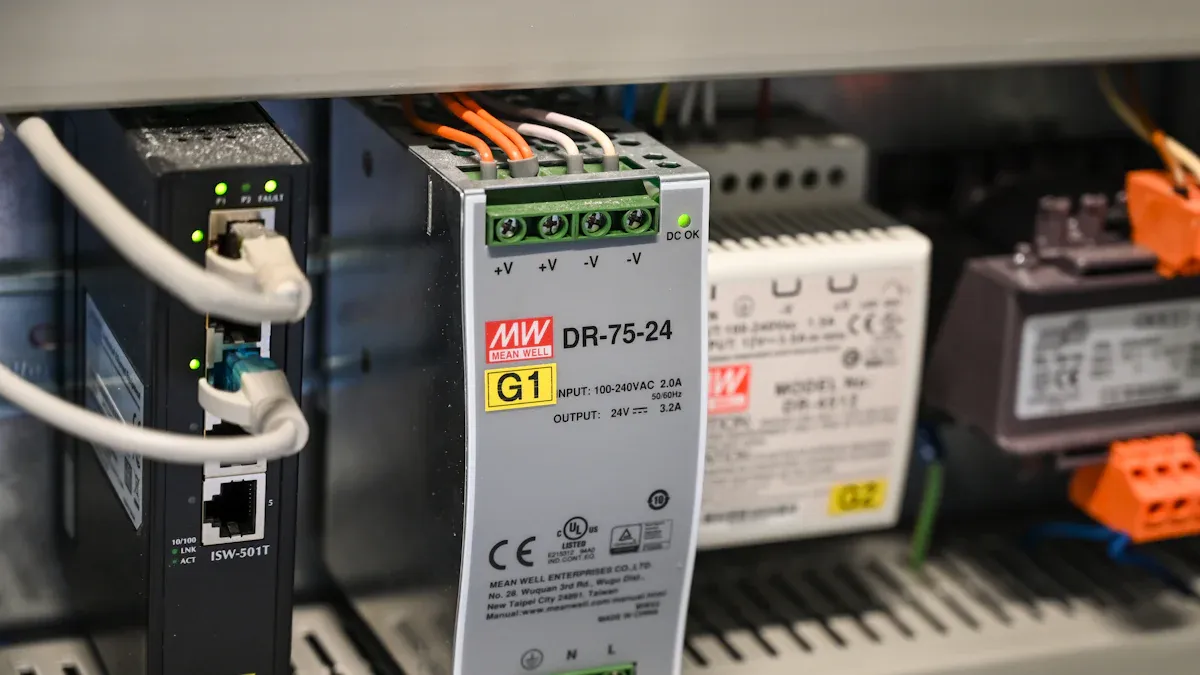
Processing Power and Performance
Industrial PCs are powerful because of their advanced processors. They handle tough tasks like data analysis and multitasking. PLCs, on the other hand, are made for simpler jobs. They control machines and check sensors. This makes PLCs great for quick tasks but not for complex ones.
Feature | Industrial PCs | PLCs |
---|---|---|
Processor Performance | Strong processors for hard tasks | Limited power for simple tasks |
Application Handling | Runs many programs at once | Built for specific machine tasks |
Advanced Technology Support | Works with AI and machine learning | Focused only on control tasks |
Note: Use an industrial PC for heavy computing. For simple control tasks, a PLC works fine.
Memory and Storage
Industrial PCs have more memory and storage than PLCs. They store large amounts of data for analysis and databases. This makes them perfect for managing complex information. PLCs, however, store only the basic data needed for machine control.
Industrial PCs can:
Analyze complex data.
Log large amounts of information.
Run databases and work with SCADA software.
PLCs are reliable for specific tasks but lack big storage. If your project needs advanced data handling, industrial PCs are better.
Flexibility and Scalability
Industrial PCs are flexible and can grow with your needs. You can upgrade their hardware or software easily. For example, you can add new features or expand their abilities. PLCs are easy to reprogram but can’t grow much beyond their original design.
Industrial PCs offer:
Easy upgrades for future needs.
Support for many networking systems.
Flexibility for different tasks.
Tip: If your project might expand later, choose industrial PCs for better scalability.
Hardware Integration
Industrial PCs are great at working with other hardware. They run many programs and languages like Python and C++. This helps them combine control, data collection, and connectivity. They also connect to cloud services for real-time data use.
Feature | Description |
---|---|
Compatibility | Runs advanced programming languages and multiple programs. |
Integration | Connects to cloud services for better efficiency. |
Environment | Built to handle tough conditions like heat and dust. |
PLCs are reliable but lack the advanced features of industrial PCs. They focus on specific automation tasks.
Real-Time Operation
Both industrial PCs and PLCs work in real time but in different ways. Industrial PCs improve production by monitoring and controlling processes. They collect data to fix problems and boost efficiency. PLCs are best for fast input and output tasks, reacting instantly when needed.
Feature | Industrial PC (IPC) | Programmable Logic Controller (PLC) |
---|---|---|
Functionality | Handles multitasking and advanced jobs | Focused on quick machine control |
Data Visualization | Offers detailed displays | Limited graphics |
Integration | Links factory and business systems | Works alone for automation |
Performance in Complex Tasks | Great for heavy computing | Best for fast, simple tasks |
Industrial PCs:
Manage and monitor production lines.
Reduce mistakes and improve productivity.
Analyze real-time data to avoid downtime.
PLCs:
Handle fast inputs and outputs well.
Provide reliable control for specific tasks.
Note: For multitasking and detailed visuals, pick industrial PCs. For quick, real-time control, PLCs are the better choice.
Advantages and Disadvantages
Benefits of Industrial PCs
Industrial PCs are great for handling tough automation tasks. They have strong processors that can manage hard jobs like data analysis and multitasking. These PCs connect well with IT systems, helping factories and businesses work together better.
They are also very flexible. Industrial PCs can use many programming languages, making them good for custom projects. They save money for big systems, especially when managing many tasks at once. You can control them remotely, which helps you keep track of operations from anywhere.
Feature | Industrial PCs |
---|---|
Advantages | Handles hard tasks like AI and multitasking |
Connects easily with IT systems | |
Allows remote control and monitoring | |
Saves money for big operations |
Tip: Pick industrial PCs if your project needs advanced computing or flexibility.
Drawbacks of Industrial PCs
Industrial PCs have some downsides. They might need extra protection to survive tough factory conditions. This can make them cost more at first. They also need more care because their hardware and software are complex.
Another problem is their high starting price. While they save money for big systems, smaller projects might struggle with the cost. Industrial PCs may not work as well as PLCs in extreme heat or heavy shaking.
Feature | Industrial PCs |
---|---|
Limitations | Might need extra protection for tough conditions |
Needs more care and maintenance | |
Costs more upfront for smaller projects |
Note: Think about your budget and environment before choosing an industrial PC.
Benefits of PLCs
PLCs are very reliable and tough, making them perfect for factories. They can handle heat, shaking, and other hard conditions. They work fast, giving quick and accurate control over machines.
PLCs are great for managing specific tasks. They are best for safety jobs where steady performance is needed. Industries like car-making and manufacturing use PLCs because they are precise and adaptable.
Industry | Key Benefits of PLCs in Automation Projects |
---|---|
Automotive | Precise control for car-making and electric vehicle production |
Manufacturing | Easy to scale, customize, and adapt for different needs |
Market Dynamics | Strong focus on automation and Industry 4.0 projects |
Tip: Choose PLCs for jobs needing fast and reliable machine control.
Drawbacks of PLCs
PLCs have limits too. They are not as powerful as industrial PCs, so they can’t handle hard tasks. They are less flexible because they are made for specific factory jobs. This makes them unsuitable for multitasking or advanced computing.
Another issue is their cost for big systems. While PLCs are good for small tasks, scaling them up can get expensive. Security can also be a problem, as standard PLCs may not handle new cyber threats well.
Aspect | Standard PLCs | Purpose-Built Controls |
---|---|---|
Performance | Reliable but not good for hard tasks | Made for specific factory needs |
Flexibility | Works well but not for advanced jobs | Designed for special tasks |
Security | May face cyber risks | Built with better safety features |
Note: For projects needing advanced computing or growth, PLCs might not be the best choice.
Use Cases for Industrial PCs and PLCs
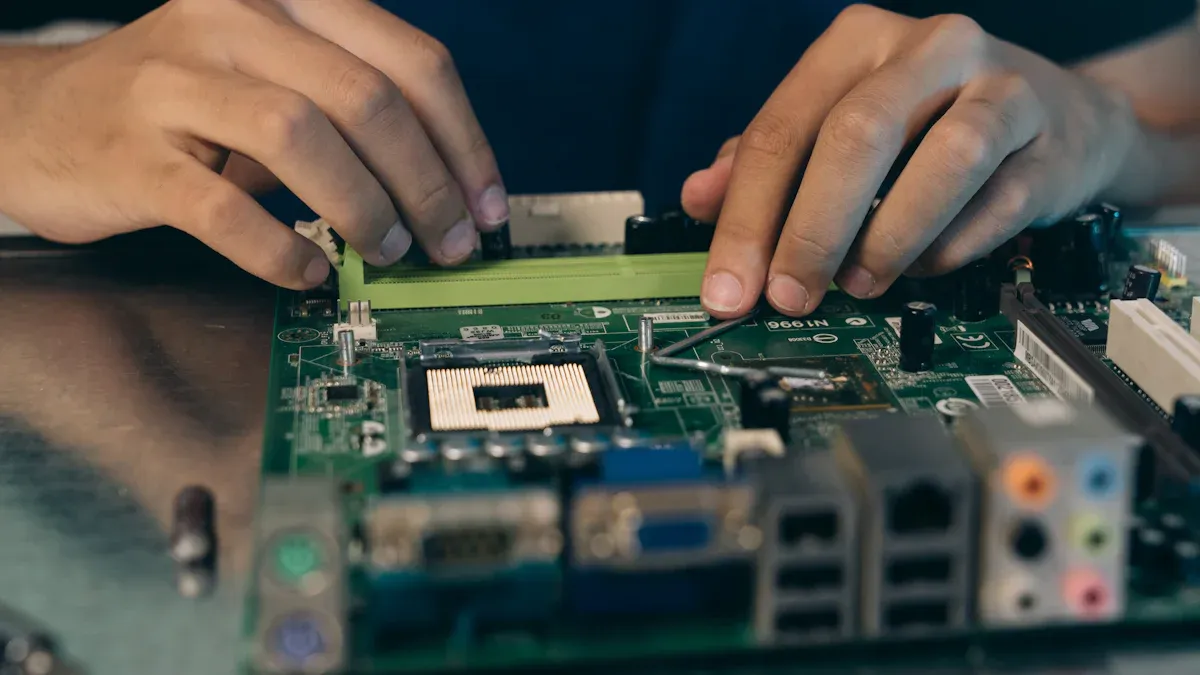
Applications of Industrial PCs
Industrial PCs are great for tough computing and flexible tasks. They are used in factories to they handle both control and complex jobs like:
Real-time analytics: Crush sensor data to spot production bottlenecks.
AI vision systems: Automate quality checks (e.g., finding defects in car parts).
Harsh environments: Oil rigs, food plants – anywhere dust or moisture would kill a regular PC.
Typical ROI: Factories using IPCs report 20% less downtime (via predictive maintenance) and 15% faster inspections (with machine vision).
Applications of PLCs
PLCs are perfect for jobs needing accuracy and dependability. They are used in quality checks, inspections, and sensor control. For example:
Quality checks: PLCs measure product size or weight and remove bad items.
Inspection tasks: They make sure inspections happen in the right order and time.
Sensor control: PLCs use sensors to keep product quality high.
Sorting and rejecting: They sort products and remove ones that don’t meet standards.
Process control: PLCs track quality trends and warn workers about problems.
These uses show how PLCs keep factories running smoothly. Their real-time abilities ensure efficient and reliable operations.
When to Use Both in a Hybrid System
Using both industrial PCs and PLCs together can be very effective. Industrial PCs handle data tasks like analysis, while PLCs control machines in real time. For example, in a smart factory, an industrial PC can study production data, while a PLC controls machines precisely. This teamwork improves efficiency and allows advanced tech like IoT and AI to work seamlessly.
Tip: Choose a hybrid system when you need both strong computing and reliable machine control.
Cost and Security Factors
Initial and Long-Term Costs
Industrial PCs cost more upfront because they are built tough. They last longer and work in harsh places, saving money later. For example, their strong design means fewer replacements are needed.
PLCs are cheaper to start with, so they’re good for small jobs. But making a PLC system bigger can cost more. They are reliable but less flexible. Adding hardware or software for complex tasks raises costs.
Tip: Think about your project’s size and needs before choosing.
Maintenance and Upgrades
Industrial PCs are easier to fix and upgrade. You can change parts like memory without stopping work. They also work with new software, staying useful for a long time. This makes them a smart choice for changing needs.
PLCs are strong but need experts for repairs. Upgrading them takes time because you may need to reprogram or change hardware. Still, their tough design means fewer repairs, even in rough conditions.
Security Considerations
Security is very important in automation. Industrial PCs connect to networks, so they face more cyber risks. Strong firewalls, secure access, and regular checks help keep them safe. A hack could leak data or stop work.
PLCs are safer from cyberattacks but not completely safe. For example, a U.S. water plant was hacked in 2023. To protect PLCs, use strong passwords, separate networks, and limit access.
Note: Update both systems often to fix risks and follow rules.
Choosing Between Industrial PCs and PLCs
Key Factors to Consider
When picking between an industrial PC and a PLC, think about your needs. Industrial PCs are great for tough jobs like multitasking and data analysis. PLCs work best for simple, repeated tasks like controlling machines.
Next, check the environment where it will be used. Industrial PCs handle heat, dust, and tough conditions. They are also good in places like oil and gas industries, where corrosion is a problem. PLCs are built to handle shaking and bumps, making them perfect for factory floors.
Finally, consider if you need upgrades later. Industrial PCs are flexible and can grow with new tech like IoT. PLCs are less flexible but are reliable for specific tasks.
Application Type | Description |
---|---|
Industrial Automation | Controls and monitors production lines, works in tough environments. |
Medical | Used in operating rooms to manage equipment, resists disinfectants. |
Oil and Gas | Handles equipment in extreme conditions, resists corrosion and high heat. |
When to Choose an Industrial PC
Pick an industrial PC if you need strong computing and flexibility. These systems are great for showing data, real-time monitoring, and connecting with IT systems. For example, in factories, they can control machines and analyze data at the same time.
If your work involves advanced tech like AI or machine learning, go with an industrial PC. It supports many programming languages and runs complex software. It also connects to cloud services, making it useful for modern industries.
When to Choose a PLC
Choose a PLC for fast and steady machine control. It works well in places needing precision, like car factories or quality checks. PLCs are also great for safety tasks because they perform reliably in tough conditions.
For repeated tasks like sorting or removing bad products, a PLC is a smart choice. Its strong design ensures it lasts long, making it a trusted tool for factory automation.
Knowing how Industrial PCs and PLCs differ helps you choose wisely. Industrial PCs are great for flexible tasks and complex computing. PLCs are better for dependable and quick machine control. Think about what you need, like performance, cost, and use. If you want something adaptable and expandable, industrial PCs are a good choice.