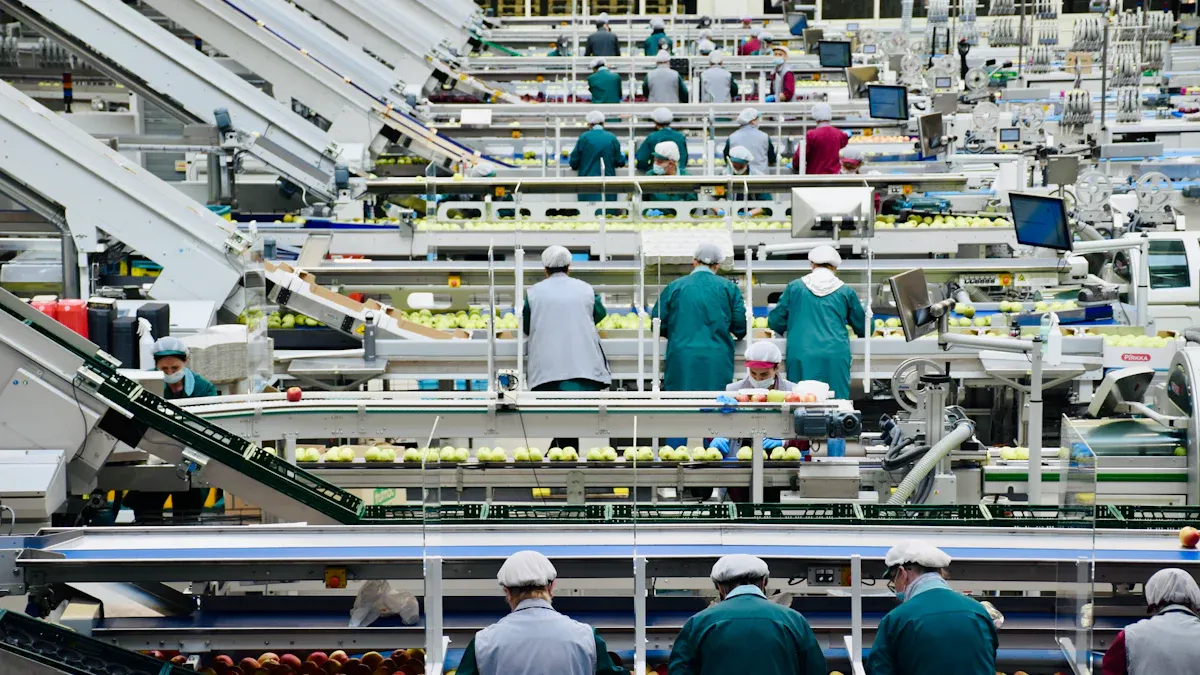
Industrial panel PCs have transformed the food and beverage industry, making production faster, safer, and more efficient. These powerful tools help reduce waste, improve hygiene, and ensure products meet the highest standards. By streamlining processes and lowering contamination risks, they not only improve product quality but also strengthen customer trust.By streamlining processes, enhancing food safety, and lowering contamination risks, industrial panel PCs improve product quality and reinforce customer trust.
Key Takeaways
Industrial panel PCs make food and drink production faster and safer. They cut down waste and help prevent contamination.
These PCs monitor in real-time, solving problems quickly. This boosts production speed and lowers the number of defects.
Their tough design reduces breakdowns, perfect for tough places like oil plants and cleanrooms.
Improving Efficiency with Industrial Panel PCs
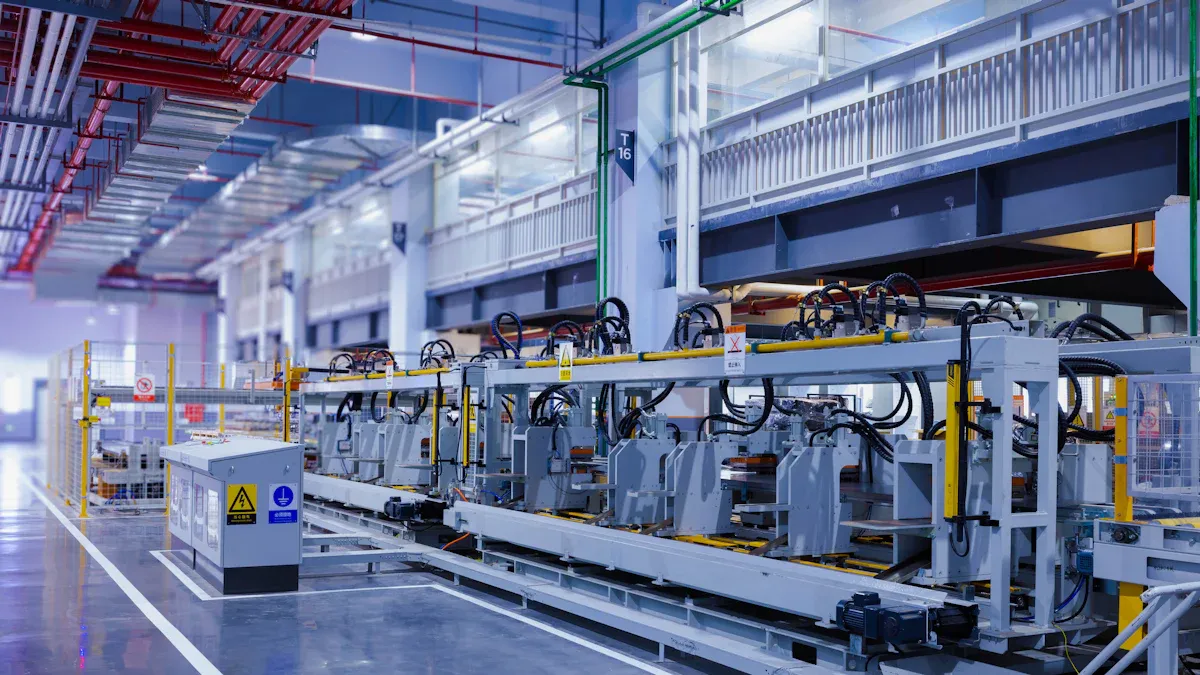
Industrial panel PCs help make food and drink production faster. They simplify tasks, reduce delays, and keep things running smoothly. Let me explain how they do this.
Real-Time Monitoring and Data Collection
Real-time monitoring with industrial panel PCs revolutionizes production workflows. These devices collect data from machines and sensors, providing instant updates on every step. This enables quick identification and resolution of potential issues, such as preventing spoilage when a temperature sensor detects a problem.
Real-time monitoring drives significant improvements in key metrics such as Overall Equipment Effectiveness (OEE), which can increase by up to 50%. Predictive maintenance, powered by real-time data, has been shown to reduce downtime by 50%, while production speeds can increase by 15-20% and defect rates drop by 30-40%, according to recent industry studies. These results show how real-time tracking improves operations.
Metric | How It Helps Production |
---|---|
Overall Equipment Effectiveness (OEE) | Better with less downtime, cut by 50% |
Production Rates | Faster by 15-20% with real-time adjustments |
Defect Rates | Fewer defects, down by 30-40% |
Speeding Up Line Operations with Smart Panel PCs
Smart panel PCs accelerate production by incorporating intuitive touch screens that simplify decision-making. With quick access to real-time data and early problem alerts, these systems help prevent costly delays and keep production moving smoothly.
One example is the Valano IP105-150 industrial panel pc features a clear screen, fast response time, and stable performance. Its real-time monitoring capabilities make production lines not only faster but also more reliable, enhancing predictive maintenance efforts.
Steady performance
Quick response
Real-time data for better management
Early problem warnings to save money |
Minimizing Downtime with Rugged Design
Downtime can halt production and lead to significant losses. Industrial panel PCs minimize this risk with rugged designs that withstand extreme heat, cold, and moisture. Their durability ensures continuous operation, even in harsh environments.
Strong features like wide temperature ranges (-20°C to 60°C) and sturdy builds cut downtime by 40%. This makes them perfect for tough jobs like oil refineries and cleanrooms.
Feature | How It Reduces Downtime |
---|---|
Rugged Design | |
Temperature Range | Handles -20°C to 60°C |
Best Uses | Oil refineries, cleanrooms |
By combining real-time tracking, smart tools, and tough designs, industrial panel PCs make food and drink production better. They boost speed, reliability, and quality in every step.
Ensuring Quality Control and Compliance
Maintaining high quality and compliance is critical in food and beverage production. Industrial panel PCs play a key role by monitoring processes, tracking critical parameters, and reducing errors. This ensures products meet strict safety standards and regulatory requirements.
Watching Important Conditions Closely
It’s important to check things like temperature and pressure carefully. Industrial panel PCs make this simple and accurate. They link to sensors and show live data on screens. I can see exact numbers and act fast if something’s wrong. For example, if storage gets too warm, the system warns me. This stops food from spoiling and keeps it safe.
These PCs let me set limits for important conditions. If a number goes too high or low, alarms go off. This helps avoid problems and follow food safety rules. I’ve seen how this cuts waste and makes work smoother.
Making Tracking and Records Easier
Tracking food production is very important. Industrial panel PCs make this job simple by working with control systems. They save details about batches, like ingredients and dates. I can check this info anytime, which helps during inspections.
With these systems, I can follow a product’s path from start to end. If there’s a recall, I can quickly find the problem batch. This clear tracking builds trust and follows strict industry rules.
Lowering Mistakes in Quality Checks
Mistakes happen often in quality checks. Industrial panel PCs help reduce these errors with easy-to-use screens. Workers follow clear steps shown on the screen. This keeps tasks consistent and accurate.
These PCs also handle repeated tasks automatically. For example, they measure and save data without needing workers to do it. This saves time and keeps the data correct.
Using industrial panel PCs helps me keep quality high and follow rules. They monitor, track, and automate tasks, making them very useful in food and drink production.
Advancing Automation in Food and Beverage Manufacturing
Automation has changed how food and drinks are made. Industrial panel PCs are important for making processes smarter and faster. Let me show you three ways they improve automation.
How Panel PCs Work with IoT to Optimize Production
Industrial panel PCs work well with IoT systems to improve automation. They collect data from sensors and machines and show it live. This helps workers make quick and smart choices. For example, if machine data shows a problem, workers can fix it fast to avoid delays.
These panel PCs are easy to use and combine many tasks into one system. They handle control, monitoring, and data processing together. This reduces the need for extra devices and makes work smoother. From my experience, using IoT with real-time control has greatly improved production.
Enabling Predictive Maintenance
Predictive maintenance is another big benefit of industrial panel PCs. They use real-time data and smart tools to predict when machines might break. This stops unexpected downtime and ensures repairs happen only when needed.
Evidence Description | Key Points |
---|---|
Industrial computers process real-time data and use smart analytics. | This helps predict problems early and reduces downtime. |
Predictive maintenance improves repair schedules and saves time. | It changes repairs from reactive to planned, making systems more reliable. |
Industrial computers are tough and handle harsh conditions. | Their strength keeps them working, even in extreme places. |
I’ve seen how this method saves time and keeps machines running longer. In tough environments, rugged panel PCs stay reliable, even in bad conditions.
Supporting Scalable and Customizable Solutions
Portable industrial panel PCs are flexible and can grow with needs. They work for small or big factories and are easy to upgrade. I’ve used systems that can be changed for tasks like packing or tracking inventory.
For example, modular panel PCs can be customized for specific jobs. This means factories can expand without replacing everything. It’s a smart way to stay competitive in a fast-changing industry.
By using IoT, predictive maintenance, and flexible designs, industrial panel PCs have changed food and drink production. They make work smarter, faster, and more reliable, helping factories do their best.
Real-World Applications in Food and Beverage Processing
Control Systems in Beverage Bottling Lines
Industrial panel PCs make bottling lines work better. They act like the brain, keeping every step smooth. These systems control filling, capping, and labeling with accuracy. For example, if the line speeds up, the PC adjusts flow to stay consistent.
These PCs also connect with sensors and machines to improve efficiency. They collect live data, so I can spot problems fast. If a bottle gets stuck or a cap is off, the system warns me. This reduces waste and keeps production moving.
Inventory Tracking in Cold Storage Rooms
Tracking inventory in cold storage is tough but easier with panel PCs. They monitor stock levels and check temperature and humidity. I’ve used them to keep products fresh and safe.
These devices collect and analyze data to create detailed reports. This helps me plan restocking better. Their strong design works well even in freezing conditions. This ensures accurate tracking and less spoilage.
Human-Machine Interfaces in Packaging Operations
Human-machine interfaces (HMIs) have changed packaging jobs. I’ve used HMIs that make controlling tasks simple. Their easy designs help workers manage complex systems.
These interfaces bring many benefits:
Faster decisions improve productivity.
Better reports give useful insights.
Maintenance alerts stop sudden breakdowns.
Remote access helps fix problems quickly.
The SmartLink feature in some HMIs is very helpful. It shows machine data to reduce downtime. With touch screens and bigger displays, these systems are easier to use.
Feature | Description |
---|---|
Improved Productivity | Speeds up work and increases efficiency. |
User-Friendly Designs | Makes it simple for workers to operate. |
Enhanced Reporting | Gives better data for smarter choices. |
Preventative Maintenance | Plans repairs to avoid problems. |
Remote Access Support | Allows real-time fixes and monitoring. |
Using industrial panel PCs and HMIs makes packaging lines faster and better. These tools improve quality and reduce mistakes.
Industrial panel PCs have changed how food and drinks are made. They help work faster, keep quality high, and use smart tools. Their strong build and ability to follow rules make them important.
Using these tools helps factories work better, follow rules, and stay ahead in a fast-moving world.
FAQ
Why are industrial panel PCs crucial for food and beverage manufacturing?
Industrial panel PCs are designed to meet strict hygiene standards, handle harsh environments, and improve operational efficiency, ensuring food safety and reducing production risks.
How do industrial panel PCs help with food safety?
They check important things like temperature and humidity. Alerts stop spoilage and contamination, keeping food safe for people.
Can industrial panel PCs work with current systems?
Yes, they easily link to IoT devices, sensors, and controls. This makes work faster, smoother, and helps with quick decisions.